COPC-2000
COPC standard is
specifically developed for call center industry and later extended to Business
Process Outsourcing (BPO) companies as well.Unlike ISO-9001:2000, this standard uses the language used in the call
center industry and also specifies the key customer-Related Processes (KCRPs)
and Key Support Processes (KSPs) to be controlled.Further, for each type of call center and BPO
it specifies detailed metrics to be controlled in the standard.
The companies implementing COPC need to achieve some benchmark
levels to get certified.Thus it is more
performance oriented and six sigma can help achieve these benchmarks.The following criterion is used for
certification of COPC standard:
-
Meet or exceed targeted performance levels for at least 50% of the metrics, and
-
Exhibit sustained improvement in a total of 75% of the metrics.
Further, meeting targeted performance levels is defined as
meeting targets 2/3rds of the time in a six months period.
The specific
requirements of the COPC standard and the suggested application of six sigma is
as follows:
1.3
Business strategies and plans – the
financial and non-financial targets can be converted to six sigma projects and
prepare an annual project plan.
1.4
Reviewing performance – six sigma
tollgates is an effective way of reviewing and the supporting the above
improvement plans.
2.1
Developing new CSP end-user
servicing capabilities – develop Critical-to-Quality (CTQs) and
Critical-to-Process (CTPs) based on Voice of Customer and Quality Function
Deployment (QFD).
2.2
Implementing new products, services,
programs and clients – DFSS approach completely address this requirement.
2.3
Process control – FMEAs can be used
to identify high risk KCRPs and make procedures to reduce the risk of failure
and thus ensuring consistent performance to clients.Further, control charts can be used to
achieve process stability.
2.4 Process improvement – the four step approach described in 2.3.3
is similar to the DMAIC approach. DMAIC is a structured and scientific approach
to find root causes.
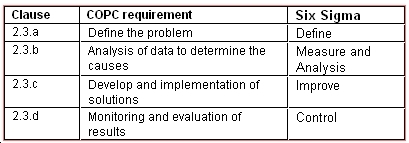
2.6
Transaction monitoring – detailed
control plans can be developed to monitor the transactions.
2.6.2
Individuals performing the monitoring
calibrated – Accuracy, repeatability and reproducibility studies can be done to
qualify the quality analysts performing transaction monitoring
2.8
Contingency planning – the FMEAs can
be used extensively to prioritize the risks and plan steps to reduce the risk
to acceptable levels.
2.9
CUIKA: Performance data to be Collected, Usable, Integrity, Known to people and lead to Actions – Six Sigma is very strong in
data management. Appropriate statistical techniques can be used to convert the
basic data into information, and then it can be used by decision makers in a
better way.Further, measurement system analysis
(MSA) techniques can be used to quantify the data integrity measures.
2.10
Data Security – the FMEAs can be used
extensively to prioritize the risks and plan steps to reduce the risk to
acceptable levels.
|